There are always two aspects to the discussion around silage harvesting costs. For the farmer, the issue is the overall cost in terms of acres harvested, or dry matter per tonne. For the contractor, the operational costs associated with the machines, and the team, are the priority.
It is important to understand the balance between how these costs affect the contractor’s ability to provide a cost-effective service to farmers while also maintaining a viable business and supporting improved farming output. For many contractors, silage harvesting is the big annual cost in their operations – while it provides a valuable boost to cash flow, that doesn’t always deliver profitability.
The ever-shortening silage harvesting season also challenges the viability of contractor services at a time of high machinery cost inflation, coupled with operator scarcity.
If cattle numbers decrease on farms, and if the area of grass silage to be harvested declines, then the viability of providing high output, self-propelled silage harvesting systems that deliver timely harvesting to ensure quality silage, will be questionable.
The discussion about the potential harvesting output from self-propelled systems often swings between fact and fiction.
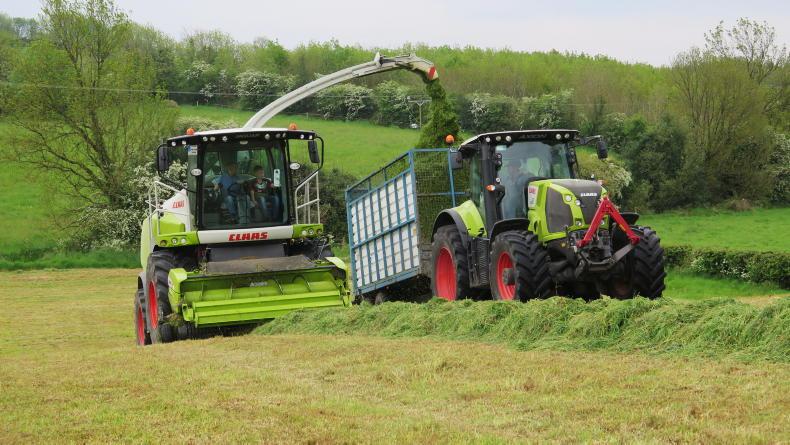
The figures of machine hours show that some machines are not achieving an output of 1,000 acres per season while others are achieving more than 3,000 acres per season.
While many contractor teams may talk of high output harvesting days where 150 acres of grass were ensiled in a day, the more typical figure is closer to 100 acres per day. This is the more achievable figure, but just not every day.
There are many ways of looking at the contractor costs and why silage harvesting charges have crept up in recent years. Increased tractor and machinery costs have meant almost a doubling in the cost of some machines in a 10-year period. So, are the current rates being quoted viable for contractors?
For this article, I’ve looked more closely at self-propelled silage harvesters and how efficiently they are being used. It is estimated that there are approximately 900 self-propelled silage harvesters working in this country. This is based on an average market of 60 machines per year entering the Irish market, between new and second-hand (40 new and 20 second-hand), plus 20% obsoletion, over a 20-year period.
Operational costs
To examine how well they are used and to assess the impact of use levels on operational costs, I’ve looked at more than 29 self-propelled silage harvesters advertised on the Irish Farmers Journal Farmers Market and with dealers, last week. Each machine listed in the adverts comes with an age, engine hour figure and drum hour figure (see Table 1 below).
These engine hour and drum hour figures are interesting as they reflect the real output of the machine. This is because the machine is only harvesting when the drum is chopping the grass and clocking up drum hours. Drum chopping hours equal acres harvested. It is only on this basis that the agricultural contractor can charge for his or her services.
It is important to note that the output or drum hours are not related to the machine brand or model and that’s obvious from Table 1.
To look at the area harvested per season over the life of the machine, I have multiplied the drum hours by a figure of 15 acres per hour and divided this number by the age of the machine. This gives an average annual machine output level in terms of acres harvested per year.
These machine performance figures also provide an insight into how machines are used, and reflect the extent to which harvesting areas on Irish farms have become more dispersed in 2024. Our table shows the key figure on the percentage of drum hours to engine hours.
The average across the 29 machines shows that they are chopping grass for 69% of their working time.
This means that for over 31% of the machine’s life it is travelling between farms or between fields or waiting for trailers in the fields. This is non-productive time in the sense that these are not drum hours and they cannot be charged to the farmer.
But they are still hours when the machine is working. In this case, travelling between jobs is still costing the contractor in terms of machine depreciation, fuel usage, tyre wear, and operator cost. Unlike other industries, agricultural contractors only charge per acre for the silage harvested, rather than per hour or tonnage and, on this basis, they typically do not charge for travel time to and from the job.
The contractor self-propelled silage harvesters have 31% of the machine time that cannot be charged to anyone. This is a cost that must be incorporated into the overall running cost of the machine.
Fragmented holdings
Irish farms are increasingly being farmed across fragmented holdings, so the farm is now rarely in one block. This trend has become more pronounced in recent years with dairy farm expansion.
Dairy farmers are renting silage land away from the main grazing platform, and the area where the silage pit is located. This results in less effective use of harvesting machines as they travel between dispersed silage fields and for the tractors and trailers that travel back to the main farmyard and silage pit.
That situation forces a more serious examination of the costs associated with transporting silage over long distances to silage pits back on the main farm from additional blocks of silage ground (see below). The movement of the harvester between these silage plots is effectively downtime in terms of charging, but not in terms of contractor costs and this is a cost factor that farmers rarely if ever are aware of.
Big power requires big fuel supplies, especially when harvesters are going the extra miles
Silage harvesting requires big power. Where there’s big power needed, there is a need for big fuel supplies. A typical self-propelled silage harvesting outfit will consume in excess of 3,000 litres during a 100 acre per day ensiling performance.
Adding distance to the silage transport operation from field to silage pit, is also an expensive extra cost. Driving tractors and trailers fully loaded at a given speed, or unloaded on the return to the field at higher speeds, means an average fuel consumption figure of 1 litre per kilometre per tractor and silage trailer both ways.
A 15km field to silage pit distance means consuming 30 litres of diesel per tractor and trailer run. If the contractor is shifting 50 acres of silage this distance, this equates to at least 50 trailer loads (using modern big trailer taking almost an acre of grass), depending on dry matter (previous rainfall, etc).
Extra fuel costs
This adds an extra 1,500 litres of fuel used at a cost of over €1 per litre after the latest Excise Duty and Carbon Tax increases ahead of the 2024 silage harvest.
Harvesting grass silage on fragmented farms and at a distance from the main silage pit, adds a significant cost to the contractor’s operation.
To ensure that the harvester can achieve that 69% chopping efficiency demands a large number of trailers for a 15km distance, up to eight or nine trailers for the job. Otherwise, the harvester will be idle to too long and reduce the drum to engine hour efficiency target.
These are not just the additional fuel costs associated with longer transport distances, but also extra costs due to additional engine hours on the harvester, when its not chopping grass but moving between silage areas. And that’s confirmed by the ratio of chopping or harvesting hours to engine hours averaging 69%.
Drum to engine hour ratio
The figures on machine hours show that some machines are not achieving an output of 1,000 acres per season while others are achieving more than 3,000 acres per season. This output is only achievable with high levels of drum hours to engine hour ratios.
In summary: an output of 100 acres per day, or almost seven hours per day of effective harvester chopping time, and an average annual machine performance of 2,600 acres of silage harvested per season (see table), converts to 26 days of harvesting work per season for an investment of over €1m in machinery.
At today’s contractor rates and with any levels of farmer debt for harvesting services provided, agricultural contractors may generate high levels of theoretical cash flow which quickly converts to high debts levels. This alone cannot sustain a viable business, which demands regular machine reinvestment, to continue to deliver high output self-propelled silage harvesting services.
There are always two aspects to the discussion around silage harvesting costs. For the farmer, the issue is the overall cost in terms of acres harvested, or dry matter per tonne. For the contractor, the operational costs associated with the machines, and the team, are the priority.
It is important to understand the balance between how these costs affect the contractor’s ability to provide a cost-effective service to farmers while also maintaining a viable business and supporting improved farming output. For many contractors, silage harvesting is the big annual cost in their operations – while it provides a valuable boost to cash flow, that doesn’t always deliver profitability.
The ever-shortening silage harvesting season also challenges the viability of contractor services at a time of high machinery cost inflation, coupled with operator scarcity.
If cattle numbers decrease on farms, and if the area of grass silage to be harvested declines, then the viability of providing high output, self-propelled silage harvesting systems that deliver timely harvesting to ensure quality silage, will be questionable.
The discussion about the potential harvesting output from self-propelled systems often swings between fact and fiction.
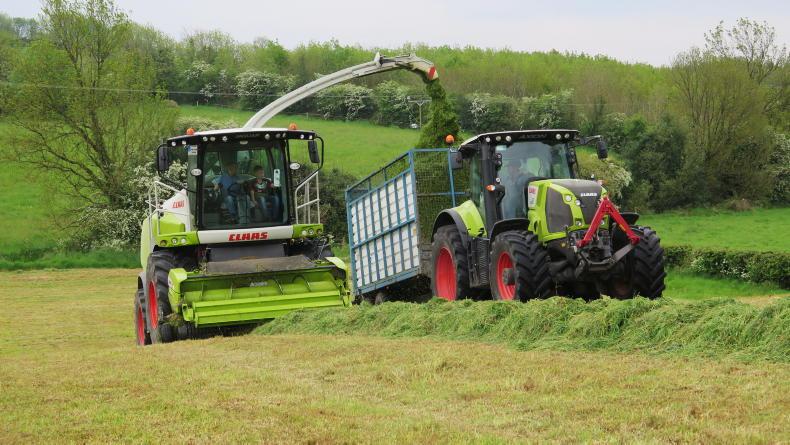
The figures of machine hours show that some machines are not achieving an output of 1,000 acres per season while others are achieving more than 3,000 acres per season.
While many contractor teams may talk of high output harvesting days where 150 acres of grass were ensiled in a day, the more typical figure is closer to 100 acres per day. This is the more achievable figure, but just not every day.
There are many ways of looking at the contractor costs and why silage harvesting charges have crept up in recent years. Increased tractor and machinery costs have meant almost a doubling in the cost of some machines in a 10-year period. So, are the current rates being quoted viable for contractors?
For this article, I’ve looked more closely at self-propelled silage harvesters and how efficiently they are being used. It is estimated that there are approximately 900 self-propelled silage harvesters working in this country. This is based on an average market of 60 machines per year entering the Irish market, between new and second-hand (40 new and 20 second-hand), plus 20% obsoletion, over a 20-year period.
Operational costs
To examine how well they are used and to assess the impact of use levels on operational costs, I’ve looked at more than 29 self-propelled silage harvesters advertised on the Irish Farmers Journal Farmers Market and with dealers, last week. Each machine listed in the adverts comes with an age, engine hour figure and drum hour figure (see Table 1 below).
These engine hour and drum hour figures are interesting as they reflect the real output of the machine. This is because the machine is only harvesting when the drum is chopping the grass and clocking up drum hours. Drum chopping hours equal acres harvested. It is only on this basis that the agricultural contractor can charge for his or her services.
It is important to note that the output or drum hours are not related to the machine brand or model and that’s obvious from Table 1.
To look at the area harvested per season over the life of the machine, I have multiplied the drum hours by a figure of 15 acres per hour and divided this number by the age of the machine. This gives an average annual machine output level in terms of acres harvested per year.
These machine performance figures also provide an insight into how machines are used, and reflect the extent to which harvesting areas on Irish farms have become more dispersed in 2024. Our table shows the key figure on the percentage of drum hours to engine hours.
The average across the 29 machines shows that they are chopping grass for 69% of their working time.
This means that for over 31% of the machine’s life it is travelling between farms or between fields or waiting for trailers in the fields. This is non-productive time in the sense that these are not drum hours and they cannot be charged to the farmer.
But they are still hours when the machine is working. In this case, travelling between jobs is still costing the contractor in terms of machine depreciation, fuel usage, tyre wear, and operator cost. Unlike other industries, agricultural contractors only charge per acre for the silage harvested, rather than per hour or tonnage and, on this basis, they typically do not charge for travel time to and from the job.
The contractor self-propelled silage harvesters have 31% of the machine time that cannot be charged to anyone. This is a cost that must be incorporated into the overall running cost of the machine.
Fragmented holdings
Irish farms are increasingly being farmed across fragmented holdings, so the farm is now rarely in one block. This trend has become more pronounced in recent years with dairy farm expansion.
Dairy farmers are renting silage land away from the main grazing platform, and the area where the silage pit is located. This results in less effective use of harvesting machines as they travel between dispersed silage fields and for the tractors and trailers that travel back to the main farmyard and silage pit.
That situation forces a more serious examination of the costs associated with transporting silage over long distances to silage pits back on the main farm from additional blocks of silage ground (see below). The movement of the harvester between these silage plots is effectively downtime in terms of charging, but not in terms of contractor costs and this is a cost factor that farmers rarely if ever are aware of.
Big power requires big fuel supplies, especially when harvesters are going the extra miles
Silage harvesting requires big power. Where there’s big power needed, there is a need for big fuel supplies. A typical self-propelled silage harvesting outfit will consume in excess of 3,000 litres during a 100 acre per day ensiling performance.
Adding distance to the silage transport operation from field to silage pit, is also an expensive extra cost. Driving tractors and trailers fully loaded at a given speed, or unloaded on the return to the field at higher speeds, means an average fuel consumption figure of 1 litre per kilometre per tractor and silage trailer both ways.
A 15km field to silage pit distance means consuming 30 litres of diesel per tractor and trailer run. If the contractor is shifting 50 acres of silage this distance, this equates to at least 50 trailer loads (using modern big trailer taking almost an acre of grass), depending on dry matter (previous rainfall, etc).
Extra fuel costs
This adds an extra 1,500 litres of fuel used at a cost of over €1 per litre after the latest Excise Duty and Carbon Tax increases ahead of the 2024 silage harvest.
Harvesting grass silage on fragmented farms and at a distance from the main silage pit, adds a significant cost to the contractor’s operation.
To ensure that the harvester can achieve that 69% chopping efficiency demands a large number of trailers for a 15km distance, up to eight or nine trailers for the job. Otherwise, the harvester will be idle to too long and reduce the drum to engine hour efficiency target.
These are not just the additional fuel costs associated with longer transport distances, but also extra costs due to additional engine hours on the harvester, when its not chopping grass but moving between silage areas. And that’s confirmed by the ratio of chopping or harvesting hours to engine hours averaging 69%.
Drum to engine hour ratio
The figures on machine hours show that some machines are not achieving an output of 1,000 acres per season while others are achieving more than 3,000 acres per season. This output is only achievable with high levels of drum hours to engine hour ratios.
In summary: an output of 100 acres per day, or almost seven hours per day of effective harvester chopping time, and an average annual machine performance of 2,600 acres of silage harvested per season (see table), converts to 26 days of harvesting work per season for an investment of over €1m in machinery.
At today’s contractor rates and with any levels of farmer debt for harvesting services provided, agricultural contractors may generate high levels of theoretical cash flow which quickly converts to high debts levels. This alone cannot sustain a viable business, which demands regular machine reinvestment, to continue to deliver high output self-propelled silage harvesting services.
SHARING OPTIONS: